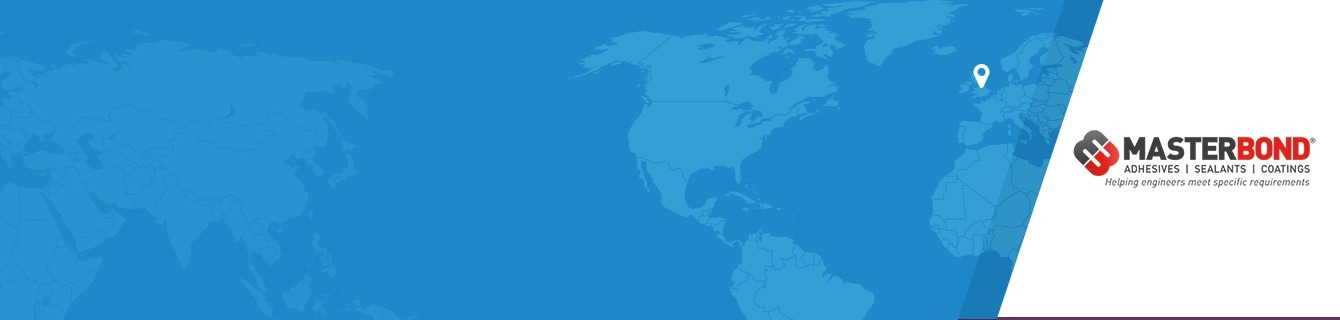
In this interview, Shira Weiner describes the features and benefits of medical-grade adhesives for medical device manufacturing.
What are some of the characteristics of medical-grade adhesives?
Medical-grade adhesives, sealants, and coatings are designed to meet the needs of medical device manufacturers. Specific grades are formulated to meet USP Class VI standards for biocompatibility and/or ISO 10993-5 requirements for non-cytotoxicity.
They are formulated to withstand sterilization such as radiation, ethylene oxide, and cold sterilants with select compounds capable of resisting repeated autoclaving and hydrogen peroxide sterilization. Additional performance properties may include optical clarity, thermal stability, thermal conductivity, the ability to bond to difficult substrates, and more.
What types of medical devices need such adhesives?
Medical-grade epoxies are used in a host of applications, including but not limited to dental equipment, diagnostics, disposable and reusable devices, monitoring systems, respiratory devices, surgical instruments, medical electronics, and prosthetics.
Image Credit: Master Bond EP3HTSMed is a one-component, electrically conductive, biocompatible epoxy system.
Do you have any examples of where your epoxy systems have been used?
Master Bond has collaborated with universities, national laboratories, and other research institutions to create innovative adhesive compounds that meet their specific application requirements. As a result, Master Bond products are cited in over 300 research articles published in peer-reviewed scientific journals. They are also cited in over 800 US and international patents.
In one such example, researchers sought to devise and test a novel microchannel array with 16-20 channels to assess the extent of nerve regeneration that is critical to the long-term efficacy of prosthetic devices.
Immunofluorescence was employed to determine the extent of motor nerve regeneration within the microarray channels. The devices that the team used featured Master Bond EP3HTSMed. This study was published in the International Journal of Physical Medicine and Rehabilitation.1
Can you tell us more about the application and how EP3HTSMed was used in the device?
The authors used standard fabrication methods in the construction of the microarray devices.1 Photolithography was used to define a SU-8 mold onto a silicon wafer — a 200 mm layer of Elastomeric polydimethylsiloxane (PDMS) was then spin-coated onto the mold and then thermally cured.
The spin-coated PDMS layers were removed, and this process was repeated to create multiple PDMS layers that were then stacked, aligned, and bonded. Metallic tracing, integrated into a ribbon cable, was used to electrically connect each electrode in the array via a percutaneous port to external recording and stimulating devices.
Master Bond EP3HTSMed, a silver-filled conductive epoxy meeting USP Class VI requirements, was used to secure and seal the electrical connections with the through-holes of the ribbon cable.
Pin-grid array (PGA) techniques were used to connect the microchannel array, bond pads, and the ribbon cable, with all connections being made with Master Bond EP3HTSMed, with the final interface being embedded in silicone.
To find the results of this research, and to read the full case study, click here.
Can you share another case study of an epoxy system used for a medical application involving prosthetics?
In an arthroplasty application for knee replacement, researchers used wireless sensors to monitor the prosthetic component. To do this, researchers at the University of Tennessee installed strain gauges into the prosthetic tibial component. The gauges measured the impact on the joint by reading strain data through a strain-mapping wireless sensor array that could feed information on force transmission through the joint following the knee replacement surgery.2
The sensors needed to be encapsulated with medical-grade adhesive to both protect them from damage and to form an appropriate interface between the implanted device and the bone tissue.
Of the epoxies evaluated for the encapsulation, EP30Med proved to be the best choice due to several factors: its low viscosity, non-rapid cure time, and the minimal amount of air bubbles present in the mixed epoxy during the curing process, which helped to create a durable, homogenous consistency.
The results of this research, along with the full case study, can be found here.
For more information about Master Bond adhesive systems or to discuss your application, visit www.masterbond.com.
References
- Maimon, B., Zorzos, A. N., Song, K., et al. (2016). Assessment of Nerve Regeneration through a Novel Microchannel Array. International Journal of Physical Medicine and Rehabilitation. 4:2. DOI: 10.4172/2329-9096.1000332
- To, Gary; Mahfouz, Mohamed. Center for Musculoskeletal Research The University of Tennessee. Qu, Wenchao; Islama, Syed K., Department of Electrical Engineering The University of Tennessee, Knoxville, TN. Multi-channels wireless strain mapping instrument for total knee arthroplasty with 30 microcantilevers and ASIC Technology. https://www2.warwick.ac.uk/fac/sci/eng/research/grouplist/sensorsanddevices/mbl/database/ieeesensors08/PDFs/ Papers/280_6396.pdf
About Shira Weiner
Shira Weiner is a member of the Technical Team at Master Bond Inc., a custom formulated adhesives manufacturer. She interfaces with customers identifying their unique application needs and provides product solutions for companies in the aerospace, electronics, medical, optical, and oil/chemical industries. She has a background in healthcare with a PhD in Ergonomics and Biomechanics.
About Master Bond Inc.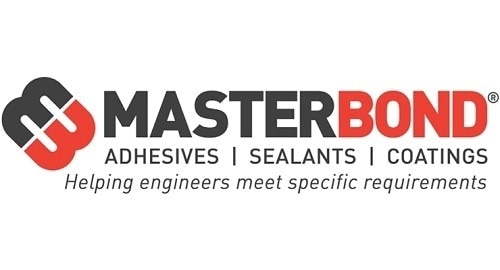
Adhesives, sealants, coatings and potting / encapsulation compounds
Master Bond is a leading manufacturer of high-performance adhesives, sealants, coatings, potting and encapsulation compounds and impregnation resins. Their product line consists of:
- Epoxy Systems
- Silicone Systems
- LED/UV Curable Systems
- Other specialty systems
Master Bond custom formulates products with specific performance properties designed for unique applications. These compounds exhibit the advanced properties required for a number of different industries, including aerospace, medical, optical, electrical, electronics, OEM and other manufacturing industries.
Adhesive compounds meet specific performance property requirements
Master Bond custom formulates products with specific performance properties designed for unique applications. Depending on the performance requirements needed, systems may be electrically conductive, electrically insulative, NASA low outgassing, resistant to high or low temperatures and thermal cycling, optically clear and so much more. Systems have been developed which offer high physical strength properties and outstanding chemical resistance even when applied on dissimilar or difficult to bond materials. Master Bond products come in a variety of different curing processes, designed for easy processing and high reliability.
Certain systems are formulated to adhere to industry standards
Master Bond grades meet different certifications such as NASA low outgassing, UL 94V-0 and UL 94V-1 for flame retardancy, USP Class VI for disposable and reusable medical devices, FDA CFR 175.105 and CFR 175.300 for food processing equipment, and more.
Master Bond is proud of being at the forefront of developing new and innovative products.
Sponsored Content Policy: News-Medical.net publishes articles and related content that may be derived from sources where we have existing commercial relationships, provided such content adds value to the core editorial ethos of News-Medical.Net which is to educate and inform site visitors interested in medical research, science, medical devices and treatments.